Operation Processes
So many Body Shops are focused on LEAN and LEAN processes as the answer to the success of their operation. Unfortunately, it may show some improvement, however never reaches the full potential as intended.
LEAN was originally designed by Toyota to improve processes within a large volume production environment. Here is an example. The CAMRY plant in Kentucky has three production lines producing over 500,000 vehicles per year! Each line produces a specific base model like the Avalon, Camry, and Lexus ES with various editions of each model handled on the main line. The emphasis here is on the volume of each line at levels of 100,000 plus. This is not what goes through a Body Shop!
Although some of the LEAN tools apply, this is not the best model to use in a body shop environment. The mix of every job is diverse. There are no two repairs that are alike! This mix creates unique challenges in the body shop environment that needs a different look to maximize success!
Identifying The Ideal System
What system is ideal for an environment that constantly has a mix of jobs that are never the same? It is found by using QRM (Quick Response Manufacturing) or in our case Re-manufacturing! QRM was founded by Rajan Suri in 1993. It takes LEAN to the next level by addressing the mix that takes place in certain types of manufacturing or remanufacturing operations. It does not just address the shop floor but all processes throughout the entire company.
To better understand the differences between LEAN and QRM, we must first know the basics of each:
So, what is LEAN?
Simply, LEAN means creating more value for customers with fewer resources. A LEAN organization understands customer value and focuses its key processes to continuously increase it. The ultimate goal is to provide perfect value to the customer through a perfect value creation process that has zero waste.
LEAN Principles
- Value. Every company needs to understand what value the customer places upon their products and services
- The Value Stream
- Flow
- Pull
- Perfection
LEAN Tools
- Value Stream Mapping
- Cellular Mfg
- Takt Time – Time Available / Demand
- One piece flow
- Pull System / Kanban
- Quick Changeover
- Ishikawa (Cause-and-Effect) Diagram and 5 Whys
- Heijunka (Load Balancing)
- Poka-yoke (Mistake Proofing)
- TPM – Total Productive Maintenance
- 5S – sort, set in order, shine, Stdize, Sustain
What is QRM?
Quick Response Manufacturing (QRM) is a companywide strategy to cut lead times in all phases of manufacturing and office operations. It can bring your products to the market more quickly and help you compete in a rapidly changing arena. It will increase profitability by reducing cost, enhancing delivery performance, and improving quality.
QRM’s focus on time as the guiding management strategy is ideally suited for companies offering high-mix, low-volume and custom-engineered products. In fact, many companies making highly customized products and/or a high variability in their product mix have used QRM as an addition to existing Lean, Six Sigma, and other improvement efforts.
LEAN works to eliminate variability….. working well with high volume production environments
QRM works on how to manage variability (a high mix, low volume, and customized) in a businesses like the Body Shop!
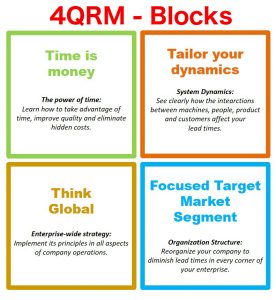
QRM Principles
- The Power of Time – QRM is Lead time focused –vs- scale and cost management
- Organization Structure – QRM has designed cells for High mix and low volume customized environment
- System Dynamics – QRM is designed for short lead times to improve capacity planning and capabilities
- Company Wide Application – QRM applies the time based management principles through all parts of the company
Shorten the total lead time of your business processes from the time you hear from customers until they get everything they expect. It’s a metric Suri defines as manufacturing critical-path time, or MCT. MCT can be used to cover everything from purchasing of raw material, components, and services all the way through order processing, production, and shipping.
Hence, on a management level, QRM advocates a mindset change from cost-based to time-based thinking, making short lead times the yardstick for organizational success.
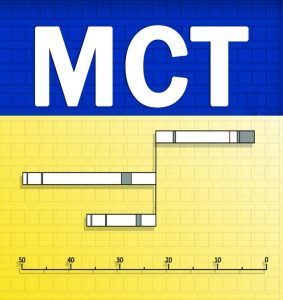
QRM Tools
MCT – Manufacturing Critical-path Time (MCT). Is defined as the typical amount of calendar time from when a customer creates an order until the first piece of that order is delivered to the customer.
A metric designed to calculate waste and highlight opportunities for improvement, MCT gives an estimate of the time it takes to fulfill an order, quantifying the longest critical-path duration of order-fulfillment activities. Most operations have actual touch time at 5-10% of the overall lead time and the other 95% is white space opportunity!
Steps in the Collision Repair Process:
- Preparation of the Estimate
- Owner Signs Repair Authorization
- Insurance Approved
- Parts Ordered
- Parts Received
- Vehicle Repair Scheduled – Express, Light, Medium, Heavy
- Vehicle Disassembled, Blueprinted & Re-Inspected
- Supplemental Damage Report (If Needed)
- Supplement Approved (If Needed)
- Additional Parts Ordered (If Needed)
- Vehicle Set on Frame Equipment (If Needed)
- Structural/Body Repairs & New Panels Installed
- Corrosion Protection Re-Applied to Repair Areas
- Metal Work Inspected
- Vehicle Prepped, Primed & Blocked
- Chemical Clean & Tacked
- Masked, Tapped & Placed in Paint Booth
- Vehicle Sealed, Basecoat, Clear Coat and Dried
- Reassembly, Wheel Alignment, Detail & Final Inspection
- Owner Notified
- Vehicle presented to the customer
What must change!
- Organization Structure must change from:
- Functional to Cellular
- Top Down to Team Ownership
- Specialized Workers to Cross Trained Team
- Efficiency/Utilization to Lead Time Reduction
- QRM Cell in all areas of the company
- System Dynamics
- Create Spare Capacity
- Optimize Batch Sizes
- Company Wide Application
- Office Operations
- Material Planning
- Production Control
- Supply Chain
So what is the Right Answer?
The right answer is a combination of both systems taking advantage of each’s strengths while keeping your eye on the prize…create “Velocity” by reducing lead time through every process throughout the organization to achieve groundbreaking customer satisfaction and high levels of profitability!
Obviously, there is a lot more to QRM. Our hope was to show you there is more out there to learn that could make a large impact on the success of your operation!
If you want to learn more about QRM, contact us and let us know!
Rajan Suri (2010) It’s About Time, New York, NY Productivity Press